What is TIG Welding: The Basics for Beginners
April 25, 2022
If you’ve just entered the world of welding, then there’s at least one phrase you’ve probably already heard a few times: ‘TIG welding is hard.’
Learning how to TIG weld does take a lot of practice, and the need for both hands makes it more difficult than MIG or stick. But that doesn’t mean it’s an impossible task that you shouldn’t even think about until you’ve mastered everything else.
TIG welding is like any other kind of welding. You should start with the basics.
What is TIG Welding?
Tungsten Inert Gas (TIG) welding is an arc welding process in which an arc is formed between a non-consumable tungsten electrode and the workpiece to create the weld.
Filler metal is added manually, though it isn’t always necessary.
An inert shielding gas is fed through the TIG torch to protect the weld from outside contaminants.
TIG welding is also known as Gas Tungsten Arc Welding (GTAW).
How Does TIG Welding Work?
You can TIG weld two different ways: with alternating current (AC) or direct current (DC). Either way, it needs a completed electric circuit running on a constant-current power source to work. All the parts of a TIG machine work together to form this circuit.
First, the TIG torch is assembled. The collet, collet body/gas lens and back cap all slot together to hold the tungsten in place in the centre. A gas shroud goes over the top to direct the shielding gas.

The TIG torch plugs into the welder, forming one part of the welding circuit. An arc is formed between the tungsten electrode and the workpiece.
Tungsten has a melting point of 3,422°C, so it can withstand the heat of a welding arc. That’s why it is a ‘non-consumable’ electrode. It doesn’t melt and enter the weld pool.
To add metal, an additional filler rod can be fed into the weld puddle by hand to form a proper weld.
That’s half of the electric circuit.
To complete the circuit, an earth clamp is needed. If you don’t have an earth clamp plugged into the machine and connected to the metal you’re trying to weld, the welder won’t even arc.
The ground also needs to be attached to clean, bare metal to work properly. Having a bad grounding will cause issues with the arc and it can become unstable or start to wander.
TIG welding is the only welding process that requires the use of both hands to create the weld, so it has a steeper learning curve than MIG or stick.
Tungsten Electrode Selection
There are a number of different tungsten electrodes, each with its own unique qualities.
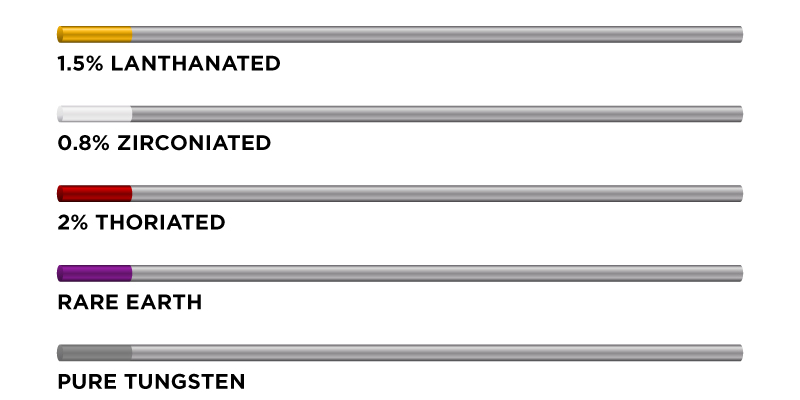
The tungsten you’ll need will depend on two things. Whether you’re welding on AC or DC and the metal you’re welding. (A bit of personal preference might also come into play.)
Check out our TIG Tungsten Selection Guide for a full breakdown of each tungsten, including pros, cons, and the distinct features of each. It’ll help you work out which tungsten is perfect for your next TIG weld.
Shielding Gas
Choosing a shielding gas for TIG is actually quite easy. The choices are pure argon, argon, and… argon.
Okay, that’s not entirely true. You can use any inert (noble) gas there is. Out of the six, four of them aren’t financially feasible. That leaves argon and helium.
TIG welding is sometimes referred to as “Heliarc” when helium gas is used. However, helium is expensive, so straight argon is the most common gas used – and it works with every kind of metal.
If you do want to know more, we’ve got an article on which gases you can use and why.
Metals
TIG welding is the most versatile when it comes to the number of materials it can weld. It can be used to weld:
- Mild steel
- Stainless steel
- Aluminium
- Copper
- Bronze
- Zinc alloys
- Titanium
Aluminium can only be welded on AC, so if you’re welding aluminium, make sure you have an AC machine such as the RAZOR TIG 200 AC/DC. Some machines, like the VIPER 185, are DC only.
Your filler metal needs to match the metal grade you’re welding, so if you’re welding 316 stainless steel, make sure you’ve got 316 stainless filler rods.
The filler rod should also be the same diameter thickness as your tungsten. For example, if you’re welding with a 1.6mm tungsten, you’ll need 1.6mm filler rods.
Polarity
So long as you have a welder that is capable, you can TIG weld in AC or DC.
Regardless of which way you want to TIG weld, it’ll be done in negative polarity or Direct Current Electrode Negative (DCEN). That means the current is negatively charged and runs from the positive to the negative.
To set up a UNIMIG welder for DCEN, plug your torch into the negative (-) panel mount and your earth clamp into the positive (+) panel mount.
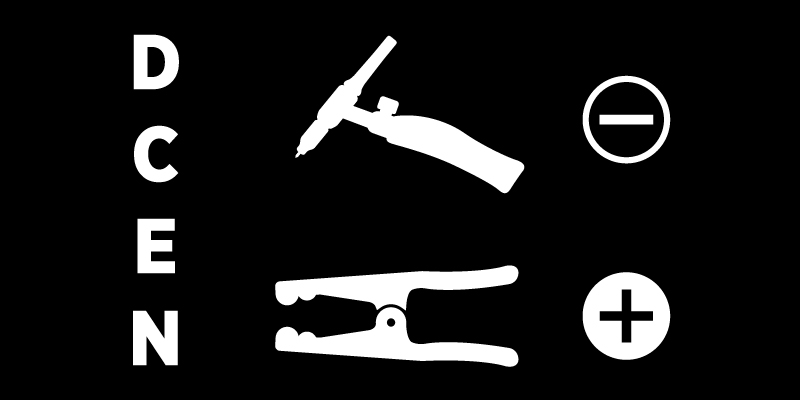
If you have an AC capable welder, you should be able to select it using the machine’s settings without changing the polarity.
Common TIG Applications and Fabrications
Despite the learning curve, TIG welding is incredibly popular thanks to its range of metal types and weld appearance.
TIG is most commonly used for:
- Thin metals – sheet metals, car panels, exhaust pipes. You name it, TIG is the best way to weld it. With the lower heat outputs, it’s perfect for welding super thin materials without the risk of burning through.
- Precision welds – The sharpened tip of a tungsten means that most TIG weld pools are smaller than MIG or stick. A smaller puddle gives the operator more control and a more precise weld, perfect for things like thin outside corner joints.
- Aluminium – TIG welding is considered the best way to weld aluminium, thanks to the cleaning properties that come with AC.
- Art – A professional TIG weld looks like a stack of dimes, making it the most aesthetically pleasing weld. Sculptures, pictures drawn by welding, coloured welds, etc., are all best done with TIG.
- Home hobby use and DIY projects – it may be the hardest to learn, but TIG welding can still be used for your DIY home projects. Bikes, trays, shelving, even the restoration project on that old car you’ve been putting off forever.
- Industries like construction, automotive, even aerospace – TIG can cover a full range of metals, it can weld thinner than MIG or stick, and filler is optional. As a result, it can be used for so many different projects: aeroplanes, nuclear plants, car parts and repairs, pipe welds.
Advantages of TIG
There are lots of reasons why TIG welding is used as often as it is, not just because it looks the best.
- It creates strong, aesthetically pleasing, quality welds. TIG welds are high quality, they look great when they’re done, and they’re just as strong as any other kind of weld.
- It’s versatile. TIG works on a huge range of different metal types (ferrous, non-ferrous, specialty) and metal thicknesses. You can also choose whether or not to use filler metal as well.
- It welds in every position. TIG welding works regardless of whether you’re in a flat, horizontal, vertical, or overhead position.
- It can weld at low amps. TIG’s ability to weld well at low amps makes it ideal for very thin applications like sheet metal or any precision welding where control is critical.
- It’s easy to see. The arc often isn’t as bright (if you’re on low amps), plus TIG torches come with additional accessories like quartz cups that make seeing your weld easy.
- It doesn’t produce spatter or slag. TIG welding is the cleanest way to weld, as it doesn’t produce any spatter or slag, plus there’s minimal smoke too. Sometimes you don’t even need to clean post-weld at all.
- It only uses one gas. TIG welding only runs with pure argon gas, so you don’t have to swap when changing metals.
- It allows for total control. The number of adjustable settings and the ability to change the amps via a foot pedal or potentiometer during the weld means you have complete control over any weld.
Disadvantages of TIG
Even though it has a laundry list of uses, TIG isn’t always the most feasible option, and there are a few downsides as well.
- It’s slow. TIG welding is the most time-consuming way to weld. Hand feeding the filler rod means it takes longer than MIG or stick.
- It takes a lot of practice. It’s well known for being the hardest kind of welding to learn, mainly because of the coordination between moving the torch and feeding the rod in at the same time.
- It’s not great for thick metals. While TIG is great for sheet metal and other thin pieces, it’s not recommended for thicker welds. For example, a 200 amp TIG machine generally caps at a maximum of 8mm, whereas MIG and stick can both usually weld up to 12mm at the same amperage/current.
- Everything has to be squeaky clean. TIG is the least forgiving when it comes to metal cleanliness. There can’t be any rust, paint, oil, dirt, etc., or you’ll end up with defects. Give your metal a wipe down or wire brush it before you start to make sure it’s good to go.
It might take some time and practice to start with, but TIG welding isn’t a skill that needs to be avoided, even if you are just starting out with welding.